The Making of Tennant20
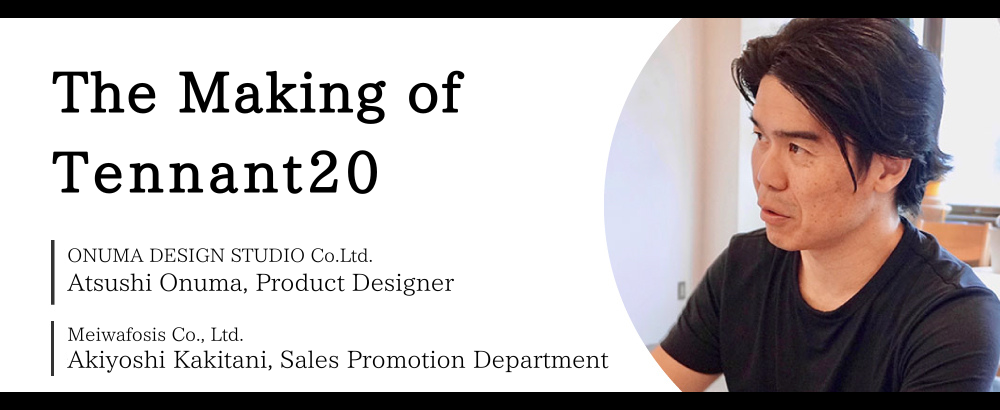

We would like to hear about your contributions to the Tennant20 project as a designer.
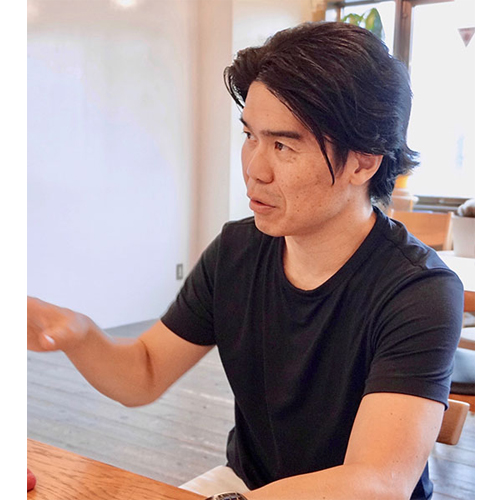
I got involved in the Tennant20 design project after Meiwafosis reached out to me at the 2020 Tokyo Innovation Exchange, hosted by the Tokyo Metropolitan Industrial Technology Research Institute. When I watched the demonstration, I thought the lid seemed heavy and difficult to handle.
I was surprised when I heard the price, as it was higher than I had expected. However, after comparing their osmium coater to similar products from other companies and learning about its data accuracy, I realized that the originality and advanced technology behind this product explain why it has earned the trust of customers for so long. I was impressed by their advanced technological capabilities.
Firstly, I sketched out my ideas. I used computer graphics at the next meeting to discuss the design with the Meiwafosis team. Even though it looked great on screen, I made a mockup to see how it would feel and fit. We talked about how it would be used in a real-world setting.
As it was an osmium coater, the Meiwafosis team had a dark color scheme in mind. I spent a lot of time thinking about how to convey a sense of luxury in the design. My goal was to create a high-end product, making “Meiwafosis” and “osmium coater” virtually interchangeable in the minds of customers.
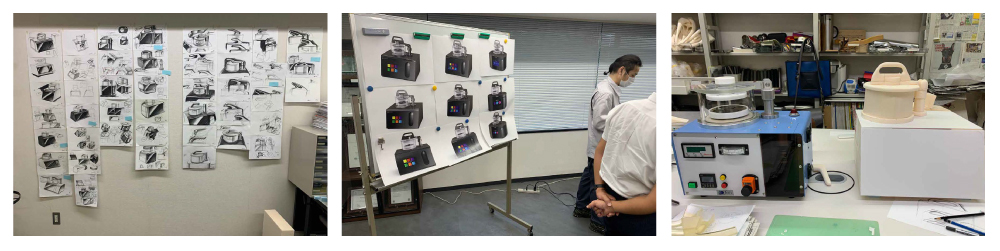
The new model is quite a departure from the Neoc, with a new body, handle, and touchscreen. What was the design philosophy behind these changes?
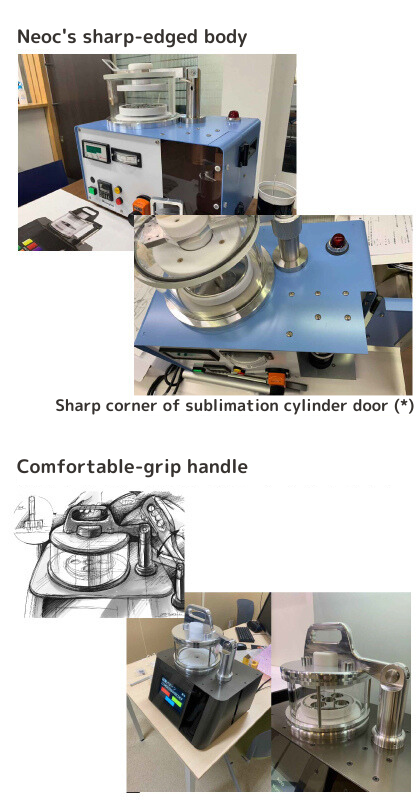
No matter what I am designing, functionality is always my top priority. When it comes to designing products for researchers and professionals, user experience is my number one concern.
As a starting point for development, I was tasked with creating a tablet-style front panel. To optimize screen visibility, I implemented an angled body design.
Furthermore, to prevent potential injuries from the sharp corner of the sublimation cylinder door*, I rounded it. Additionally, considering the weight of the door and the force required to open and close it, I designed the handle to provide a secure grip.
The design is sophisticated and well-thought-out. Were there any particular
challenges you encountered during the design process?
Steel is used for the body, so making the corners rounded for a softer feel, unlike the sharp corners of the Neoc, was a significant challenge. Since the door for the sublimation cylinder is used quite frequently, I wanted to make sure it was stable.

What led you to develop the Tennant20 as the successor to the Neoc-pro?
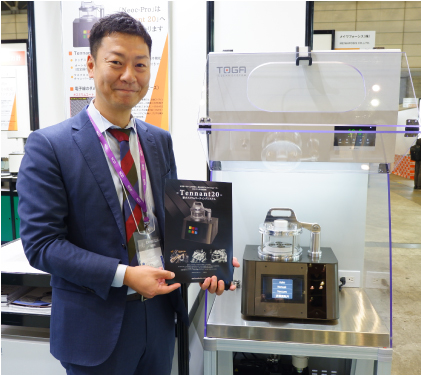
We had been considering an upgrade from the Neoc model for some time. However, we were struggling to come up with concrete plans. A significant turning point came when I attended the Tokyo Innovation Exchange 2020 at the Tokyo Metropolitan Industrial Technology Research Institute, where I met Mr. Atsushi Onuma of ONUMA DESIGN STUDIO Co.Ltd., who was serving as an equipment design advisor at the time.
If you had not met Mr. Onuma, do you think the Tennant20 would have ever been developed?
Well, I don’t think the Tennant20 would have taken its current form, or we would have even started the development. He inspired us to develop it.
What is the biggest difference between the Tennant20 and the Neoc?
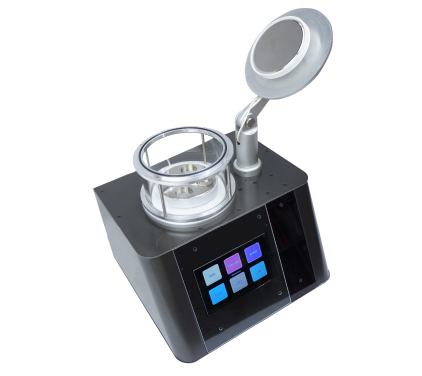
The biggest difference is in operability and safety.
The fundamental coating principle remains unchanged from the Neoc. While the Neoc focused on manual operation, we decided to add new features that allow anyone to operate the device easily and safely in response to user needs.
Furthermore, by implementing a mechanism that minimizes exposure to osmium, it is significantly safer than the Neoc. Furthermore, the Tennant20 offers a comprehensive set of features beyond those of the Neoc, including automated operation, review of operational history, passcode protection, and automatic alerts for ampule replacement.
How long did it take to develop the Tennant20?
It took about a year. The COVID-19 pandemic made it quite challenging. First, we had a meeting with Mr. Sawada of Gijinkikougei to discuss the development of the touchscreen. After that, we worked with Mr. Onuma to find a manufacturer who could produce components that met our exact specifications, and we finalized the shape and design. In November 2020, we unveiled the prototype at JASIS. Concurrently with the exterior design, we worked closely with Mr. Sawada to refine the operation and functionality through numerous iterations of improvement and testing. We devoted substantial effort to automating the processes, selecting components, and fine-tuning safety systems at each stage. To prevent issues and malfunctions arising from the drastically different user experience, we carefully analyzed the design and conducted repeated practical tests to achieve our desired performance.
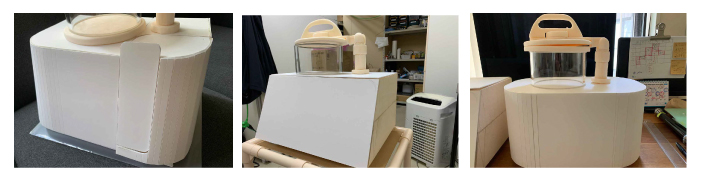
How did the customers respond to the Tennant20?
We received an overwhelmingly positive response! In particular, we’ve had a great deal of feedback from the Neoc users. Many have commented, “I was amazed at how easy it was to operate compared to the Neoc.” The easy and safe operation are significant advantages for our customers.
What are your future development plans?
We will continue to make minor updates based on user feedback. Additionally, we plan to change and update our other products, CADE (Carbon Coater) and SEDE (Soft Plasma Etching Device).
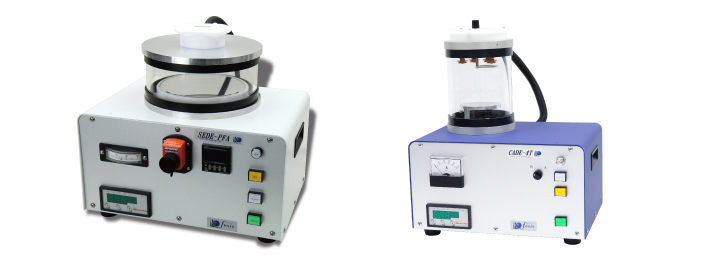
What is the future vision for the Tennant20?
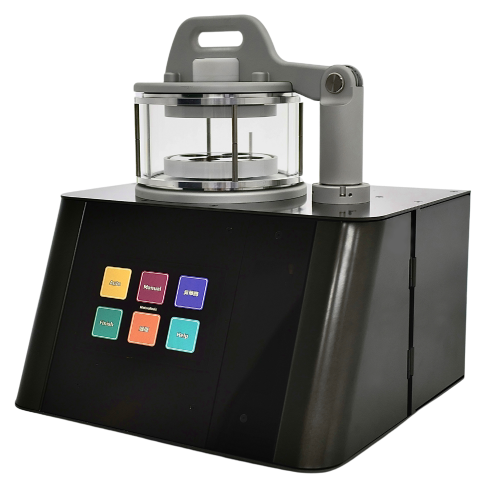
Given the improved safety and operability, we aim to expand our customer base to those who have previously avoided osmium coating systems. Moreover, osmium coating offers superior image quality for electron microscopy compared to sputtering or carbon coating. We are committed to assisting a wider range of researchers.